Inside the Craftsmanship: The Manufacturing Process of Guitar Strings
Guitar strings are more than just simple metal wires—they are the essential bridge between the player and the instrument’s voice. The manufacturing of guitar strings combines precision engineering with specialized materials science and centuries-old craftsmanship to create strings that deliver exceptional tone, playability, and durability.
1. Raw Material Selection
The manufacturing process begins with selecting premium raw materials. For electric and acoustic guitar strings, this typically includes high-grade steel wire for cores and various alloys for windings, such as:
Nickel-plated steel: Common for electric guitar strings, balancing brightness and warmth.
Phosphor bronze: Popular for acoustic guitar strings, known for its rich and balanced tone.
80/20 bronze: Another alloy used for bright, crisp acoustic sounds.
Pure nickel: Sometimes used for vintage-style electric strings with warmer tones.
Nylon or fluorocarbon: Used for classical guitar high strings.
Material quality is paramount; impurities or inconsistencies can cause breakage, tonal imperfections, or reduced longevity.
2. Core Wire Drawing
The core wire acts as the string’s backbone and is typically made from high-carbon steel wire. The wire undergoes a drawing process, where it is pulled through progressively smaller dies to achieve the precise diameter needed. This step requires accuracy, as the core’s uniform thickness affects string tension and tuning stability.
Manufacturers use computer-controlled drawing machines to ensure micron-level consistency and smooth surface finish, which contributes to a clean sound and longer lifespan.
3. Winding the String
For wound strings (all but the plain high strings), the next critical step is wrapping the core with a winding wire. This winding provides mass and flexibility that define the string’s gauge, tonal character, and feel.
Winding Materials: Common winding wires include bronze, phosphor bronze, nickel-plated steel, pure nickel, and stainless steel.
Winding Techniques:
Roundwound: The most common, with round wire wrapped tightly around the core. This produces a bright, textured tone but can cause finger noise.
Flatwound: Uses flat, ribbon-like wire for a smoother feel and mellower tone, favored in jazz and vintage styles.
Halfwound / Groundwound: A compromise that smooths roundwound strings by grinding down the outer surface.
The winding process is controlled by precision machines that maintain consistent tension and spacing. Any irregularity can cause tuning issues or uneven tone.
4. Heat Treatment and Stress Relief
After winding, strings undergo heat treatment to relieve mechanical stresses induced during manufacturing. Controlled heating processes improve flexibility and reduce the risk of premature breakage.
Stress relief also stabilizes the metal’s crystalline structure, contributing to consistent tension and tuning stability over extended playing.
5. Surface Treatment and Coating
To enhance durability and corrosion resistance, many guitar strings receive surface treatments or coatings.
Plain strings may be polished for smoothness.
Coated strings are wrapped with thin layers of polymers or specialized compounds that protect against sweat, oils, and moisture, significantly extending string life without compromising tone.
Different manufacturers have proprietary coatings, and the technology is constantly evolving to balance longevity with natural sound.
6. Cutting and Packaging
Finished strings are cut to precise lengths for each string in a set. Packaging is also critical—not just for aesthetics but to protect strings from humidity and damage during transport and storage.
High-quality packaging often includes:
Hermetically sealed envelopes or blister packs
Informative labeling with gauge, material, and tuning details
Eco-friendly materials in some modern brands
Proper packaging ensures players receive fresh, ready-to-use strings that sound their best from the first play.
7. Quality Control
Throughout the manufacturing process, stringent quality control measures are in place. This includes:
Microscopic inspection of wire diameter and surface
Tensile strength testing to prevent breakage
Acoustic testing to ensure consistent tonal quality
Random batch sampling and longevity testing
These checks maintain the high standards expected by professional musicians and discerning amateurs alike.
From selecting the finest raw materials to precision winding and protective coatings, guitar string manufacturing is a sophisticated blend of science and art. Every step influences the final product’s sound, feel, and durability, ensuring musicians can express themselves freely and reliably through their instrument.
Alice Strings
Alice Strings is a global leader in guitar string manufacturing, combining advanced technology with deep industry experience to deliver strings that meet the demands of all players. Offering a wide range of electric, acoustic, and classical guitar strings, Alice focuses on quality, consistency, and innovation.
Their commitment to superior craftsmanship and customer satisfaction has made Alice a trusted choice for retailers, distributors, and musicians worldwide. Whether you seek bright, durable electric strings or warm, rich acoustic sets, Alice provides products tailored to inspire your best performance.
Relate News
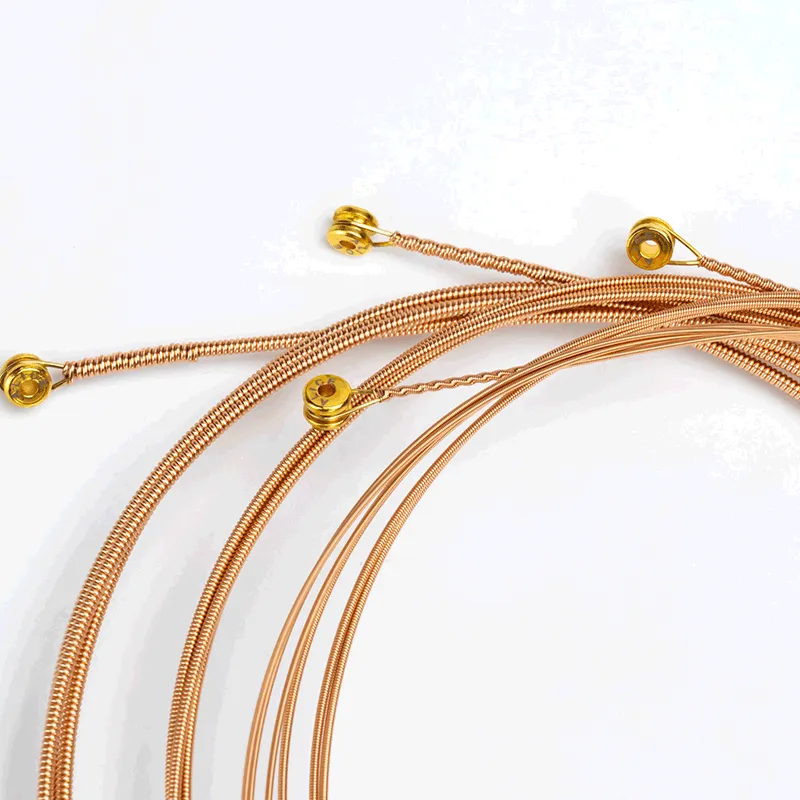
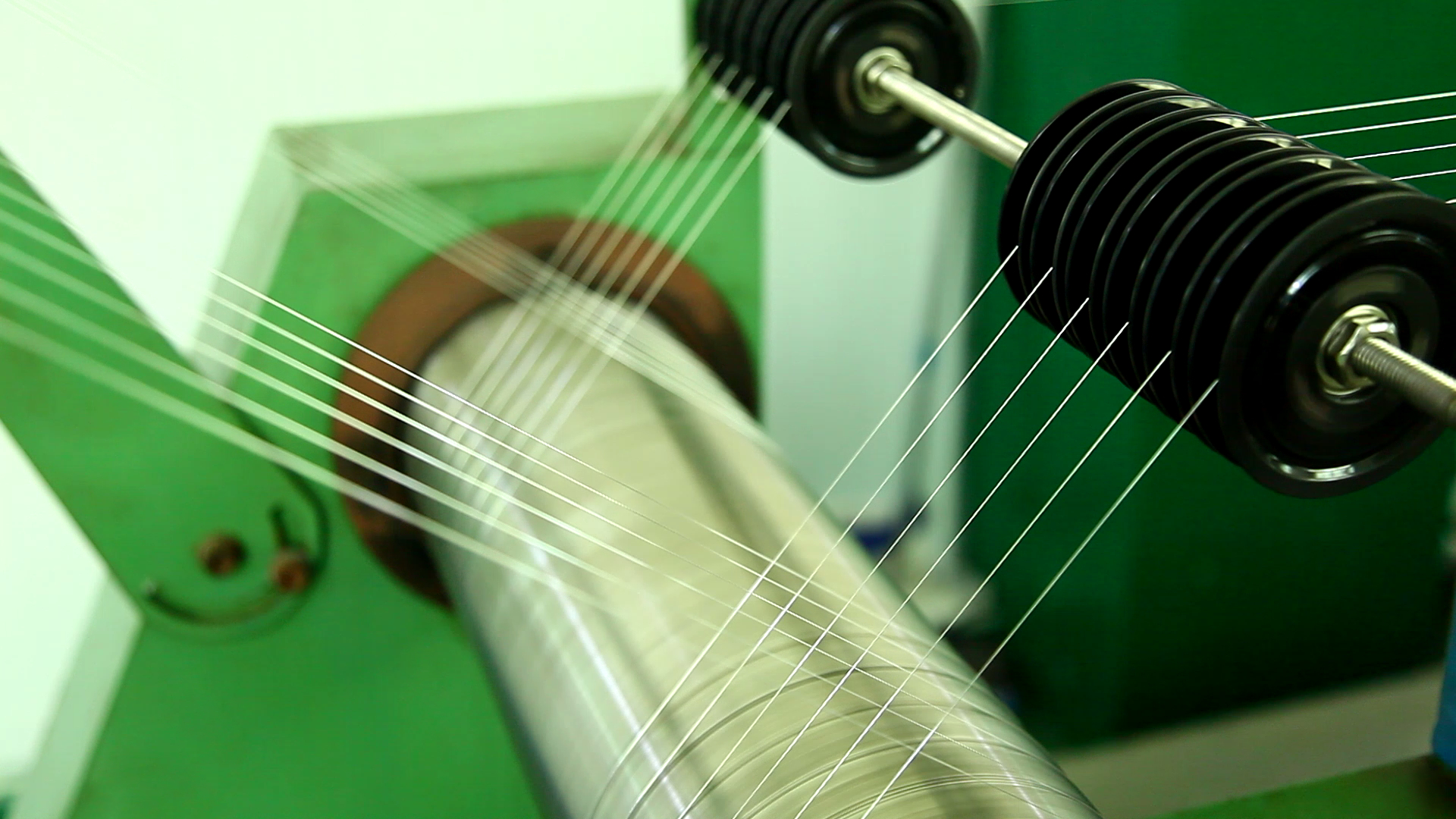
Common Guitar String Problems: How to Fix Tuning Issues, Rust, and String Breakage

Complete Guide to Guitar String Materials: Which One Is Right for You?
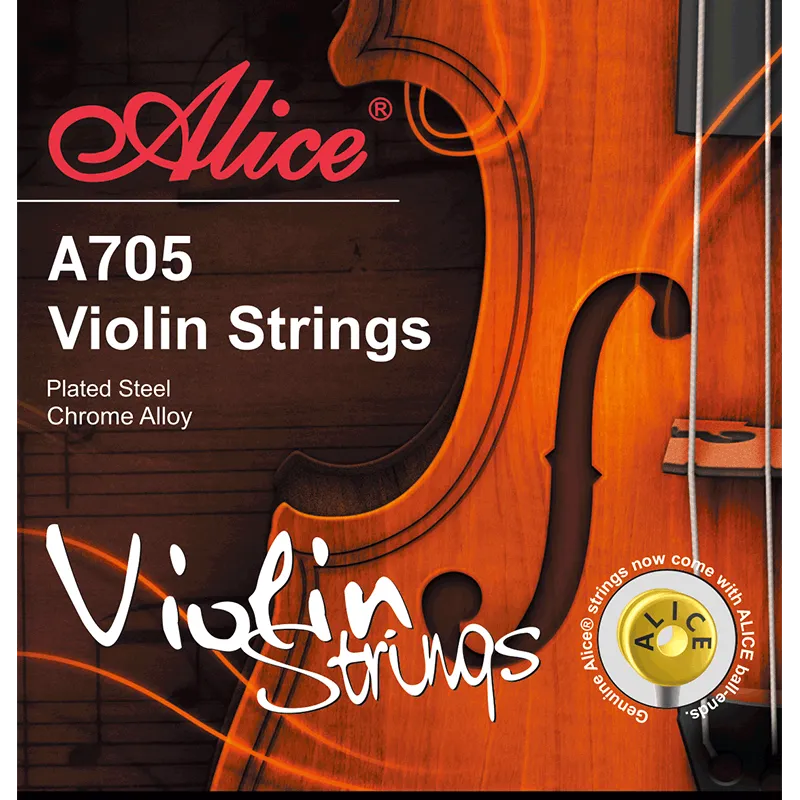
The Complete Guide to Orchestral Strings: Everything You Need to Know
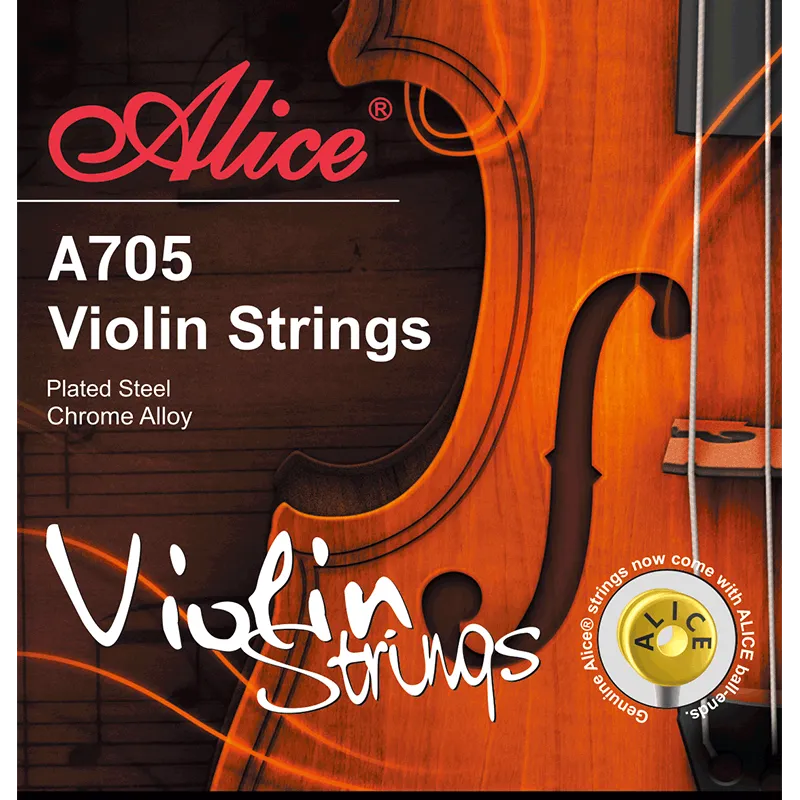
The Complete Guide to Orchestral Strings: Everything You Need to Know
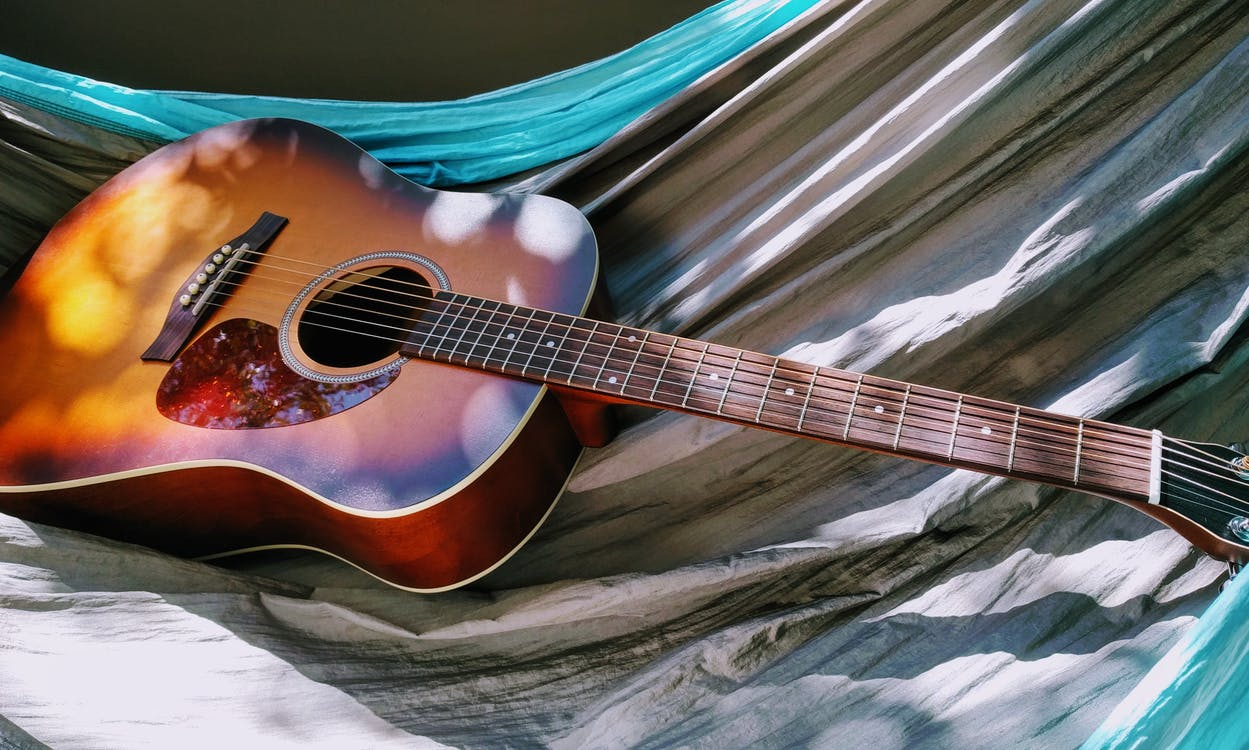
Inside the Craftsmanship: The Manufacturing Process of Guitar Strings
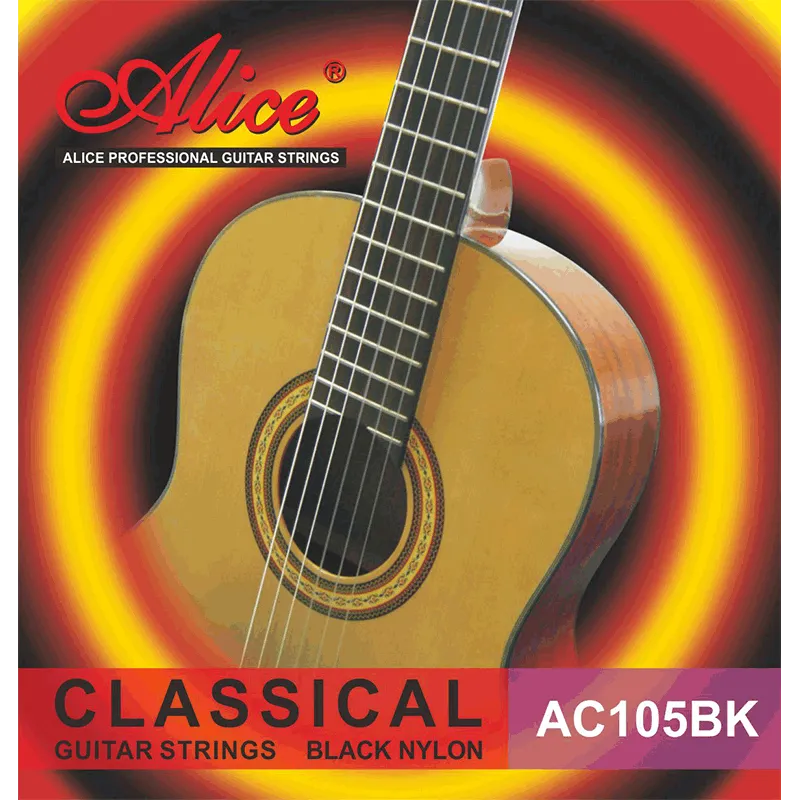
Wholesale Guitar String Purchasing: A Practical Guide for Retailers and Distributors
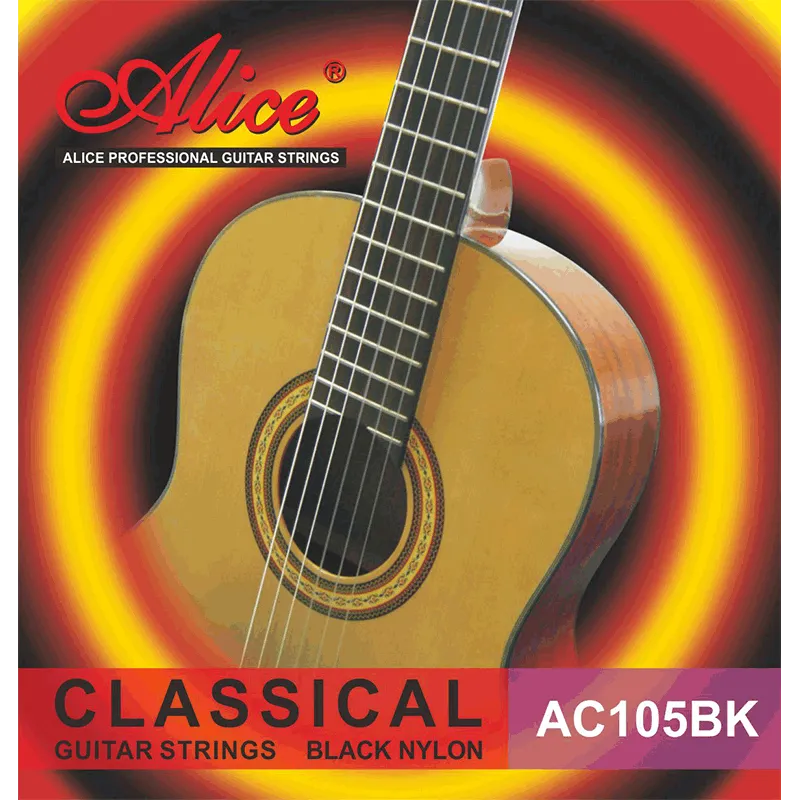
Wholesale Guitar String Purchasing: A Practical Guide for Retailers and Distributors
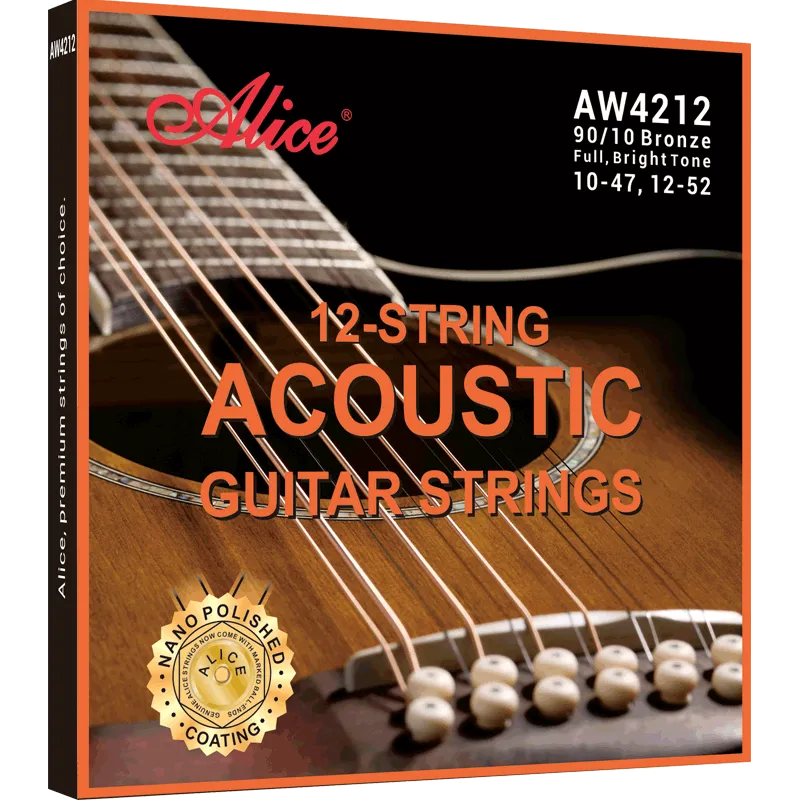
How to Choose the Right Guitar String Models for Export Markets
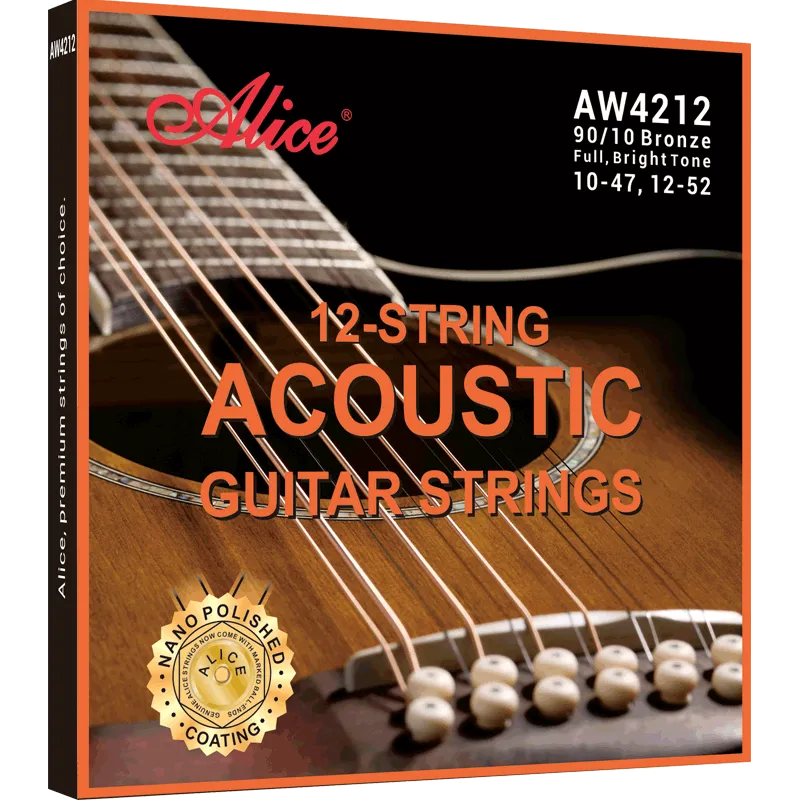
How to Choose the Right Guitar String Models for Export Markets
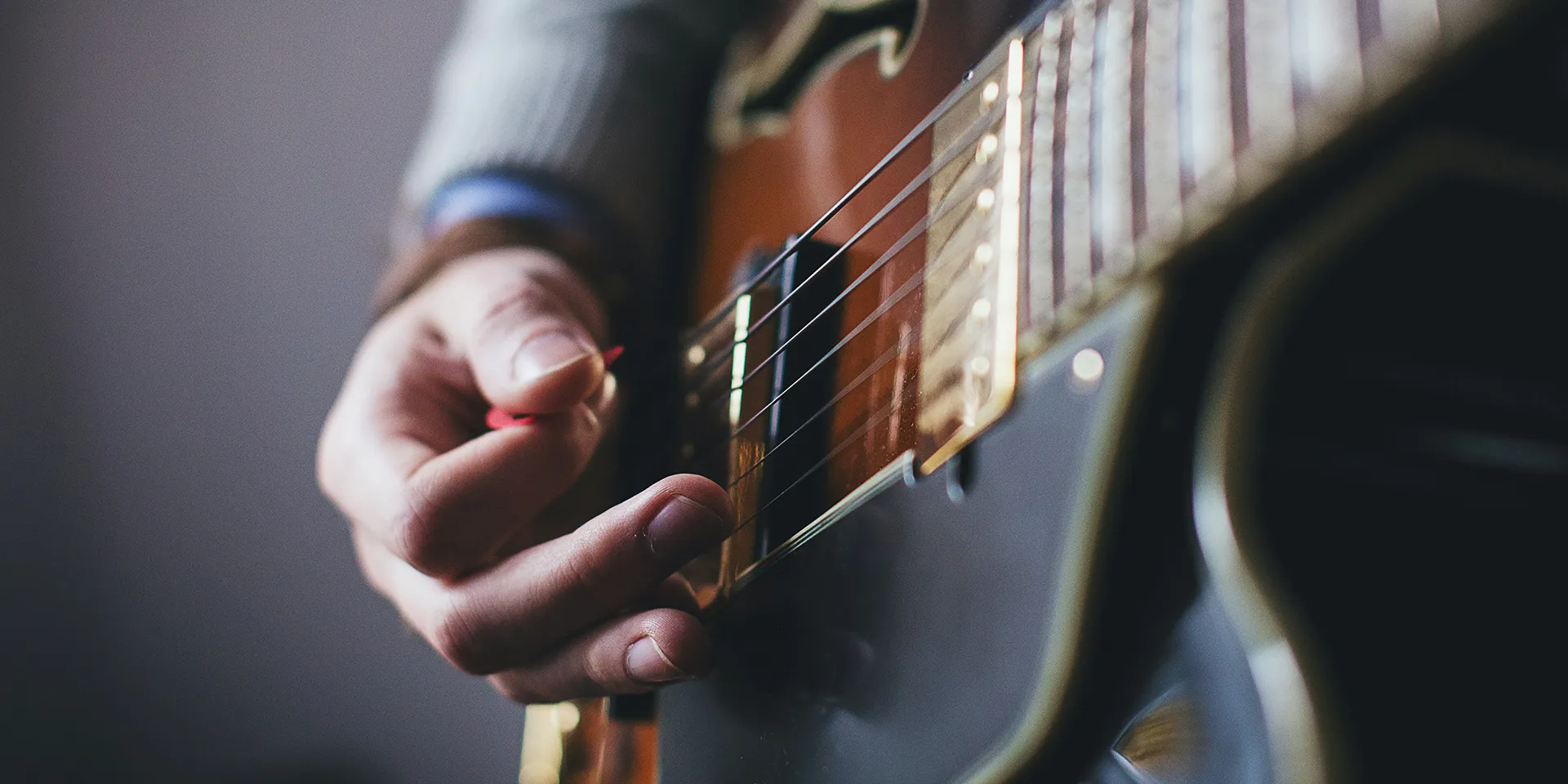
How Alice Guitar Strings Compare to Leading Brands
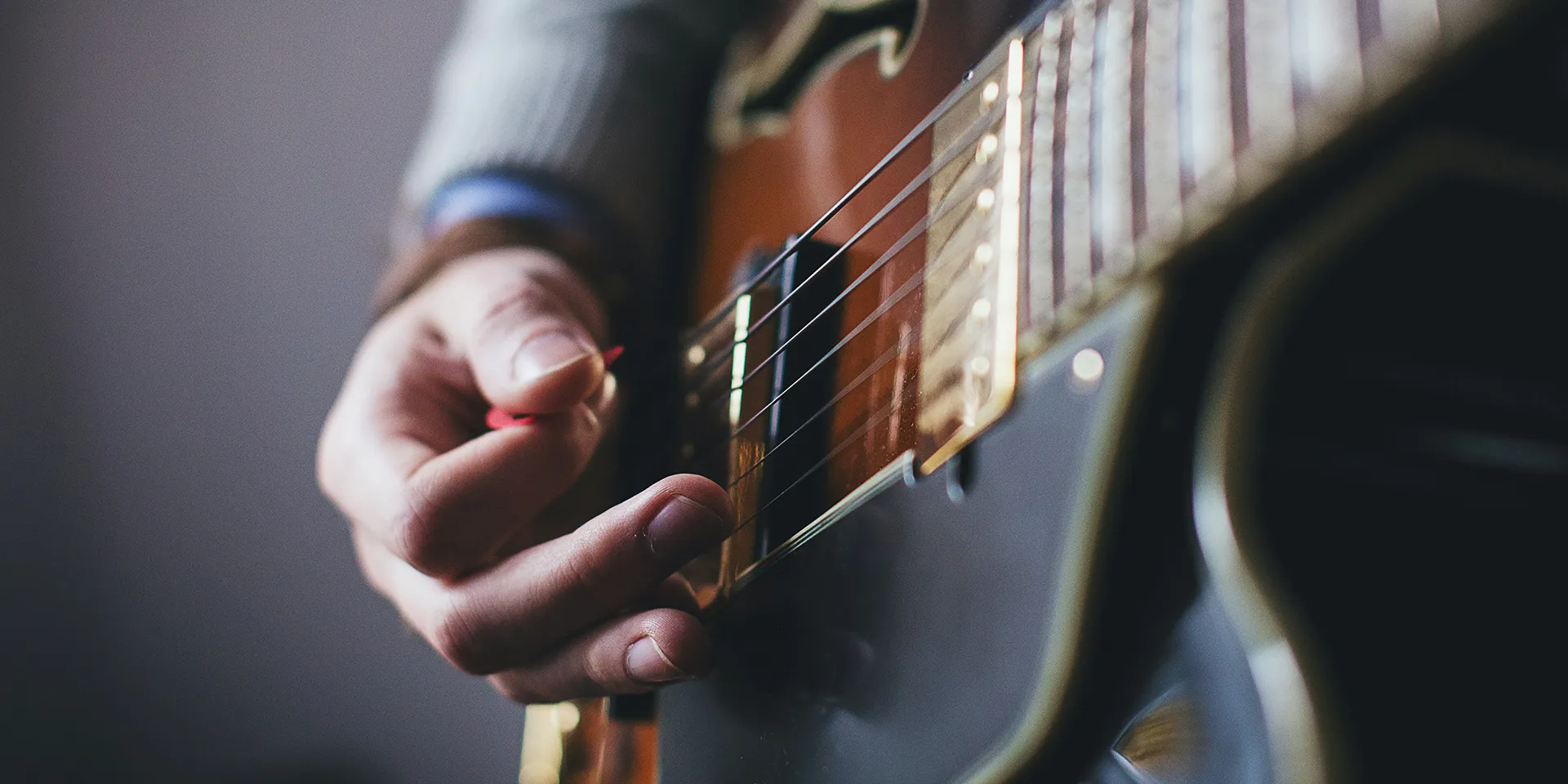